热成型及冷冲压成型工艺零件质量对比
热成型零件特点(1) 由于选择在高温下成形,不带涂层冲压零件表面存在氧化,表面质量不佳;
(2) 零件在冷却过程中由于温度分布不均匀,易产生热应力和热应变;
(3) 由于材料的高塑性,在成形过程中零件不易起皱和破裂,基本没有回弹,尺寸稳定性比较好;
(4) 材料经过加工变形和快冷,晶粒得到了细化,力学性能得到了很大的提高;
(5) 材料经过变形和硬化后,强度提高,冷冲压切边冲孔已无法达到工艺和零件精度的要求,需要利用激光或等离子切割设备完成。
冷冲压成型零件特点构件质量缺陷:起皱, 撕裂, 裂纹, 回弹, 构件翻转。冲压力受限:夹持力;深冲力。生产率低:多道次冲压。冲压机磨损:反向冲压吨位,初始接触振动,齿轮离合器咬合损失。冷冲压批量产品工艺性,冷冲压产品性能质量不均匀,不稳定。高强度钢板冷冲压成形面临的问题,在TS>=700MPa超高强钢板冷冲压成形时特别严重。
超高强钢板冷成型缺陷的重要原因有:
(1)多相组织的不均匀分布是超高强钢板在冷冲压过程中出现起皱、局部颈缩、局部撕裂的重要原因。
(2)残奥RA减少。
(3)在冷成型过程中,应变诱导残余奥氏体相变,成为马氏体。
(4)冷成型构件的TRIP效应塑性降低,抗冲撞吸收冲击功的能力随之降低。
热成型的原理和优势
金属材料加热到临界点A , 亚共析Ac3, 过共析Accm, 使铁素体,珠光体,渗碳体,全部转变为奥氏体 (P→A, F→A,Cm→A), 并保温。塑性成型同时快速降温(150 ℃/s),材料由奥氏体 (Austenite) 转为马氏体 (Martensite)。1. 热成形件抗拉强度提高2 - 3倍,更安全。2. 巨大的减重潜力。3. 可成型复杂零件,新设计可能性,一次成型,无焊接,可深冲。4. 良好的重复精度,无回弹。5. 降压机吨位 (-50%),降设备投资和使用能耗。6. 没有破裂和起皱,提高成品率 (高强度钢+10%)。
热成型模具技术要点
相对于常规的冷冲压模具仅用于零件的成型,热成形模具不但用于成型,还要用于给零件冷却淬火,因此其模具更加复杂,对模具材料选择、模具设计等方面提出了更加严格的要求,如下图所示。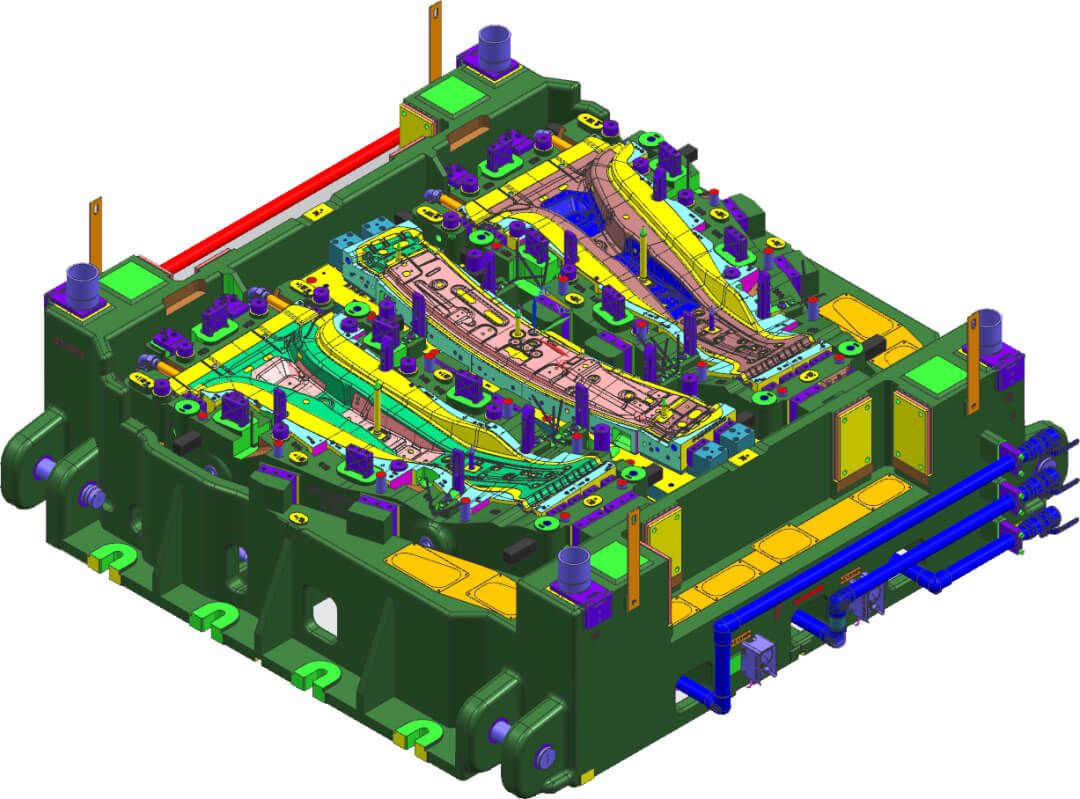
在模具材料选择方面,热成形模具材料首先要有良好热传导系数,确保钢板与模具表面之间的快速传热,实现良好的冷却功能。模具材料还要具备良好的热强度、热硬度、高的耐磨性和热疲劳性,保证模具内板冷却管道不被冷却介质锈蚀堵塞,因此国外一些热成型模具材料中都含有较高的 Ni 和 Cr。在模具材料选择时,一般要根据具体的工作情况,参照热锻造模具钢进行选择。
在模具凸凹模设计方面,不能照搬冷冲压模具的设计方法,因为热成型工艺回弹很小,几乎无须考虑回弹对零件形状的影响,另外还需考虑热胀冷缩对零件最终尺寸和形状的影响,并以此为基础设计凸凹模具的关键尺寸。
在冷却机构设计方面,冷却系统必须保证模具对零件的快速、均匀冷却,冷却管道的总体布局、形状、直径、冷却管与模具工作表面、非工作表面以及冷却管之间的距离、冷却系统密封等都是冷却机构设计的关键所在,也是热成型模具设计的最重要技术之一。设计冷却管道系统时,可以结合数值模拟技术对各管道内的冷却介质流动情况进行模拟分析,使各管道都具有相同的冷却效率,保证冷却的均匀性。
每个镶块的冷却系统相互独立,相邻镶块之间冷却水道互不连通。一般来说,模具凸起区域不利于热量向模具传递,凹形区域热量易向周围传递,在连续生产中,需在模具凸起区域设置冷却管道;在圆角过渡区容易产生热量集中,使零件该位置硬度较低。在连续生产中,需在模具圆角过渡区开设冷却管道。
热成型模具设计开发是热成型关键技术,它不同于传统的冷冲压成型模具,它是冷却协调优化设计、冷却管道加工、计算机仿真分析技术、传热模拟等技术的集成,最终达到成型、冷却、组织性能优良的完美结合。