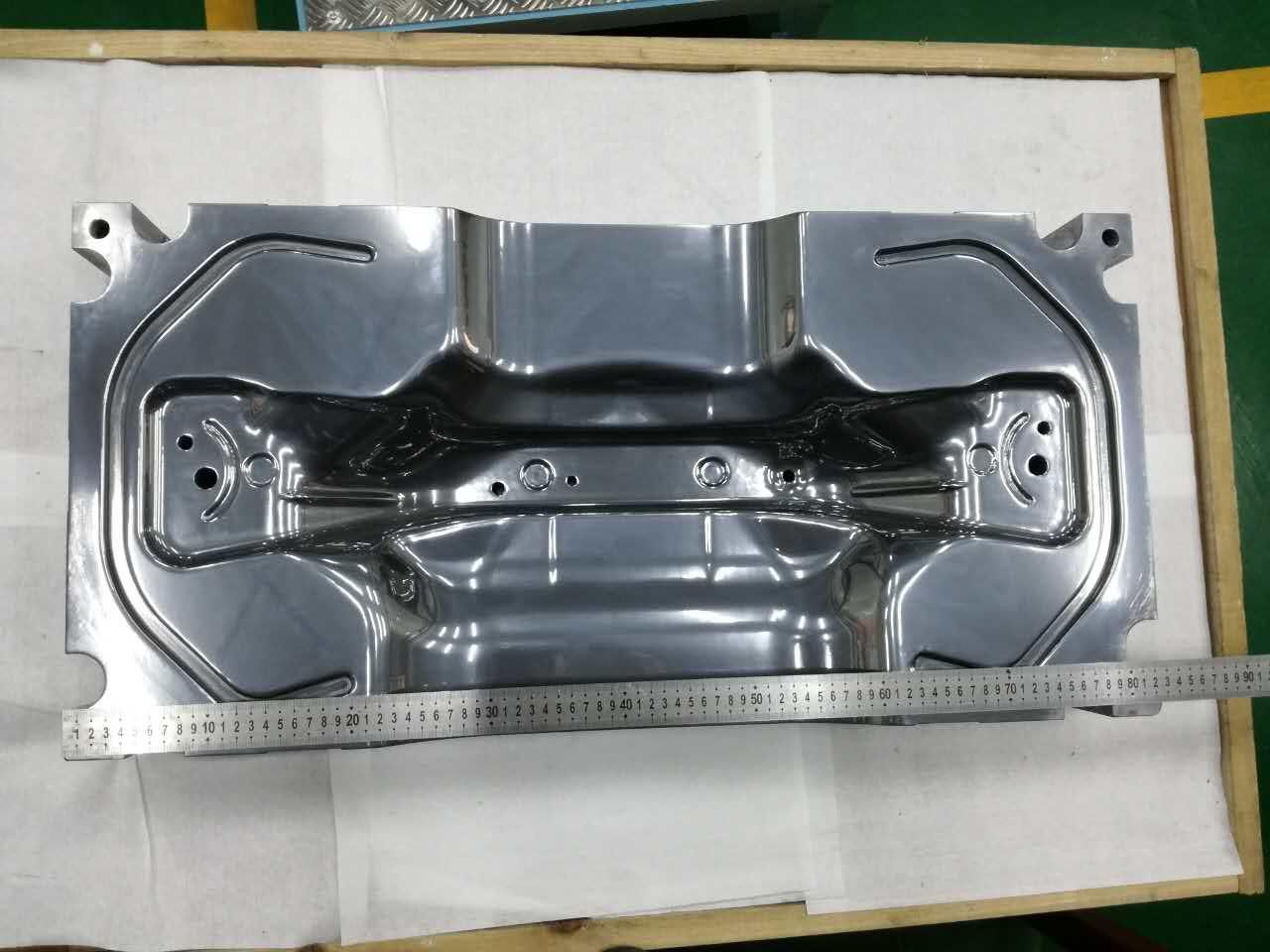
1.吸气孔的设计
抽真空成型的抽气孔设计是模具设计的关键。抽气孔应该位于片材最后贴模的位置,例如当凹模成型时在凹模的底部周围的凹陷处,当形成凸模时在凸模的底部周围。具体情况取决于成型塑件的形状和尺寸。
对于轮廓复杂的塑件,抽气孔应集中,对于较大的平面塑件,吸气孔应均匀分布。孔间距取决于塑件的尺寸。对于小型塑件,孔间距可为20 ~ 30 mm,对于大型塑件,间距应适当加大。
通常成型塑料流动性好,成型温度高时,抽气孔较小;坏料板厚度越大,抽气孔越大;坯料厚度小,抽气孔更小。总之,对抽气孔大小的要求是既能在短时间内抽出坯材与模具成型面之间的空气,又不在塑件上留下抽气孔的痕迹。
一般抽气孔直径为0.5 ~ 1 mm,最大直径不超过板材厚度的50%为宜。但对于小于0.2mm的薄板,过小的抽气孔就无法加工。
2.型腔尺寸
真空成型模具的型腔尺寸要考虑塑料的收缩率,其计算方法与注塑模具型腔尺寸相同。真空成型塑料件的收缩约有50%是在塑料件脱模后产生的,25%在脱模后1h内保持在室温下产生,其余25%在脱模后8 ~ 24h内产生。
凹模成型的塑件比凸模成型的塑件收缩率大25% ~ 50%。影响塑件尺寸精度的因素很多,除了型腔尺寸精度,还与成型温度、模具温度、塑件类型有关。因此,事先准确确定收缩率是非常困难的。
如果生产批量大,尺寸精度要求高,最好用石膏模具试制产品,并测量其收缩率,这是设计模具型腔的依据。
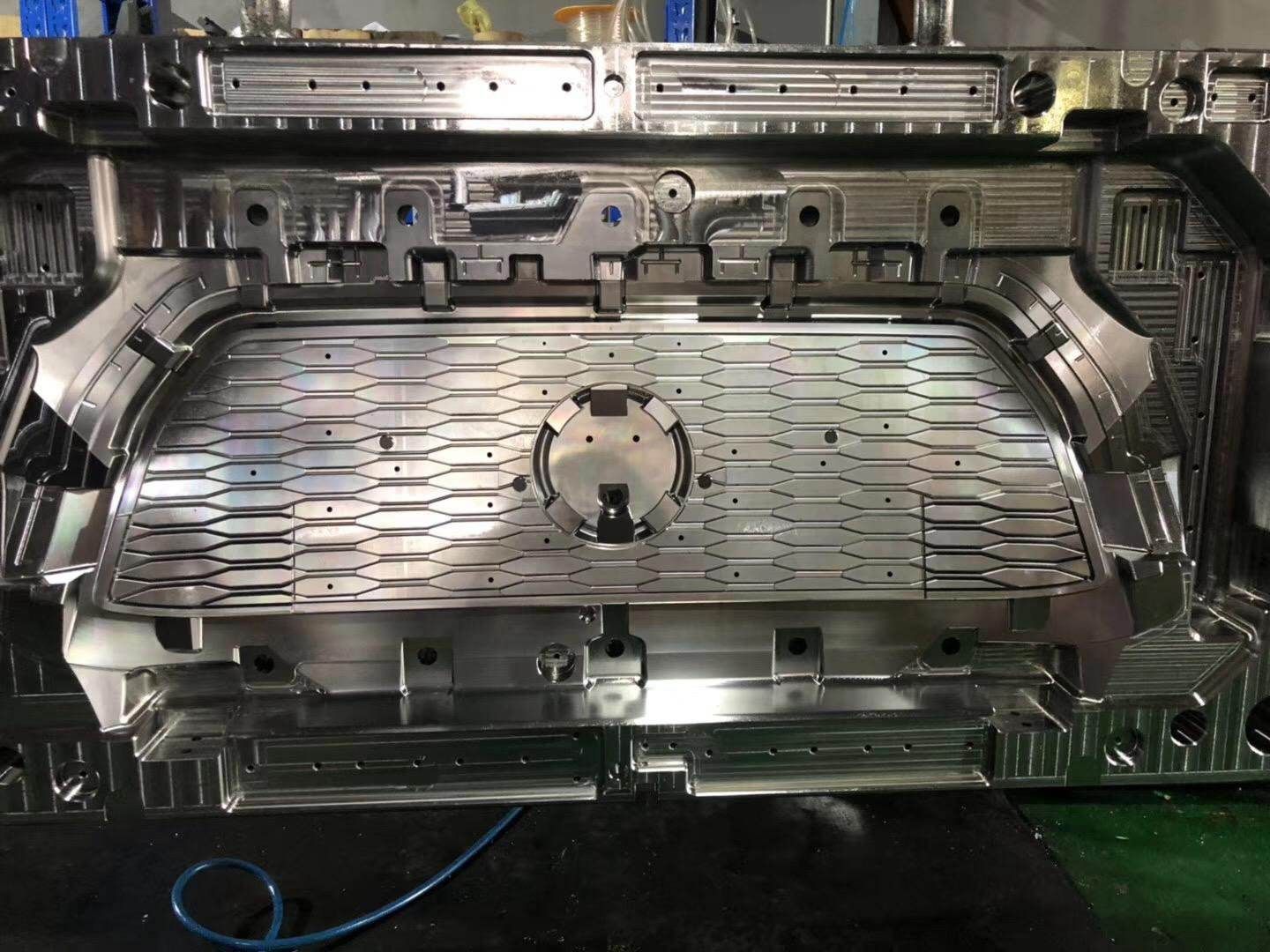
3.空腔表面粗糙度
真空成型模具一般没有顶出装置,成型后用压缩空气脱模。当真空成型模具的表面粗糙度太低时,不利于真空成型后的脱模。塑件容易粘在模具成型面上,不易脱模。即使有顶出装置顶出,脱模后还是容易变形。因此,真空成型模具的表面粗糙度高。表面处理后,最好进行喷砂处理。
4.边缘密封装置
真空成型时,为了防止型腔外的空气进入真空室,应在塑料片与模具接触的边缘设置密封装置。对于平直分型面,很容易密封塑料片与模具的接触面,但对于弯曲或折叠的分型面,则很难密封。
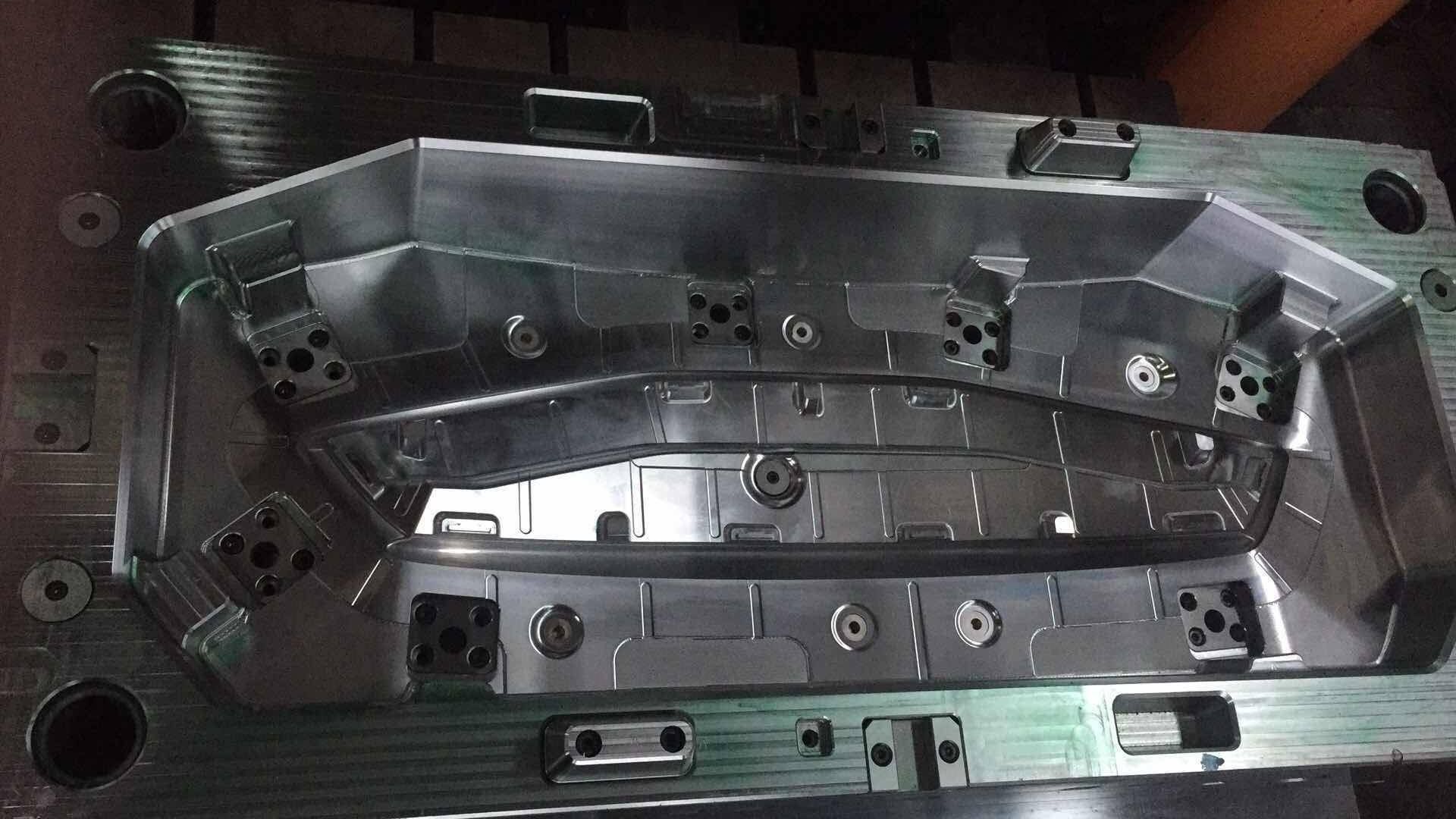
5.加热和冷却装置
用于真空成型的塑料片材的加热通常使用电阻丝或红外线。电阻丝的温度可以达到350℃ ~ 450℃。对于不同的塑料片材,通常通过调节加热器和片材之间的距离来实现不同的成型温度。通常的距离是80 ~ 120毫米。
模具温度对塑料零件的质量和生产率有影响。如果模具温度过低,塑料板与模具型腔接触会产生冷斑或应力,导致产生裂纹;模具温度过高,塑料片材可能会粘在型腔上,脱模时塑料会变形,生产周期延长。
所以模具温度要控制在一定范围内,一般在50℃左右。模具温度控制一般靠塑料与模具接触后的自然冷却,增加风冷装置加速冷却和水冷等。在模具中开设冷却通道是控制模具温度最有效、最常用的方法,冷却通道距离模具表面应在8mm以上,避免出现冷斑。
打开冷却水通道有不同的方法。你可以将铜管或钢管浇铸到模具中,或者在模具中打孔或铣槽。铣槽时,必须使用密封件并加盖板。